Want to know more about this article?
The first commercial production facility for sustainable aromatics in the world
BioBTX is now ready for the next step – the first commercial production facility for sustainable aromatics in the world, which is planned to be built in 2023. This facility will be a global first in producing sustainable aromatics on a commercial basis, enabling production of circular plastics.
BioBTX is able to take significant steps in its ambition to realize a commercial plant to produce platform chemicals from waste plastics with a full circular and sustainable process. Three existing and two new investors have decided to finance the next steps. Carduso Capital, Vries Beheer and Lynnovation followed up on earlier investments, whilst Groeifonds of the Economic Board Groningen and NOM opted for co-financing.
BioBTX is an innovative technology provider for the conversion of end-of-life materials and biomass into platform chemicals, i.e. aromatics, such as Benzene, Toluene and Xylenes (BTX). These are essential to the production of high-value specialty products, such as clothing, carpets, construction materials, medicines, cosmetics and wind turbine blades.
Producing sustainable BTX on a commercial basis
The commercial production facility is planned to be built in 2023. In December 2019, a Series B investment round was completed, enabling BioBTX to take this significant step to realizing its ambitions for a commercial plant that will use waste plastics as feedstock. The Series C investment round for building the plant will commence in 2020.
“This investment represents a significant impulse for our plans”, according to Pieter Imhof, CEO of BIOBTX. “BioBTX has a perfect fit with Northern Netherlands’ sustainability ambitions and the commercial plant will be a very valuable contribution.”
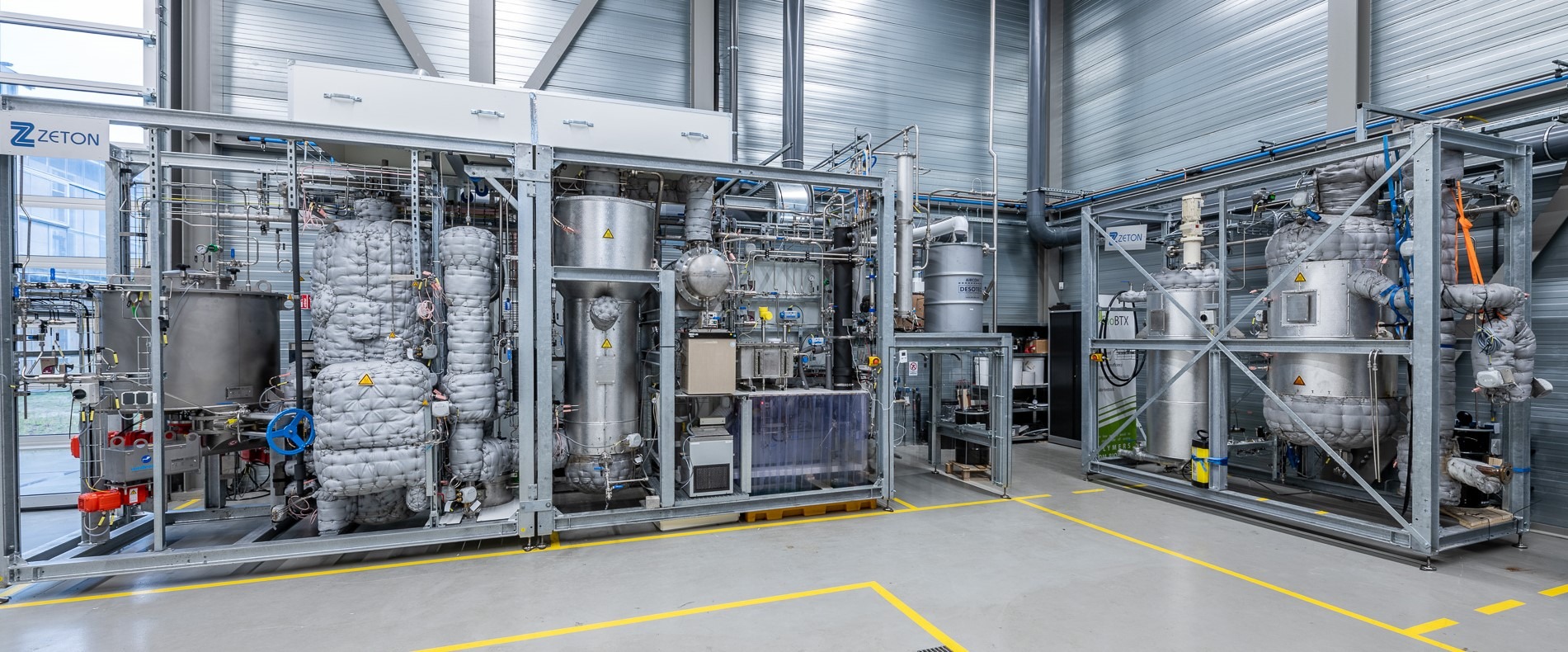
The unique technology behind BioBTX
BioBTX has developed the Integrated Cascading Catalytic Pyrolysis (ICCP) process, which contributes to a fully circular and biobased economy with a sustainable production of platform chemicals from end-of-life materials or non-food biomass. The unique integration of two steps achieves a high flexibility in feedstock and process conditions. The use of waste plastic or non-food biomass results in significant CO2 reductions, avoids incineration or landfill, and replaces the current use of oil as raw material.
The technology has been proven on lab and pilot scale with a number of patents and further IP under development. A production unit for liquid biomass with a 10kg feed/hr capacity has been operational since September 2018 with proven performance and catalyst lifetime. An additional unit for solid biomass as well as plastics & composites was installed in 2019 to demonstrate full circularity options with the ICCP technology.
Pieter Imhof continued “At BioBTX we have a science-based and low-key pragmatic approach. It has enabled us to quietly take a giant leap forward towards the production of cost-effective sustainable aromatics. This will be a gamechanger. I am very proud of what my team and our partners have achieved.”
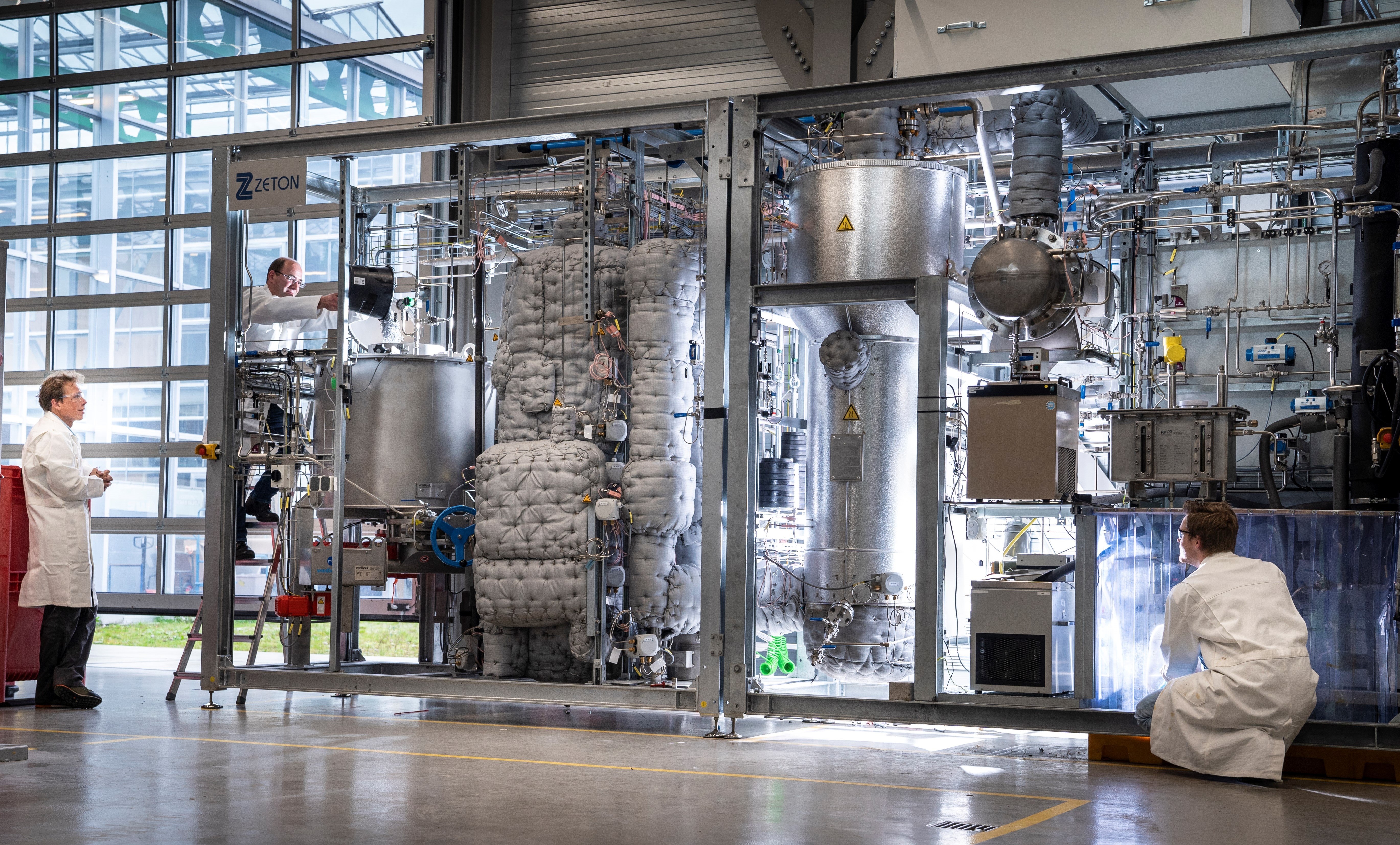
A revolutionary company
BioBTX was started by regional entrepreneurs KNN and Syncom, with technical and scientific contributions from Groningen University (RUG). The company has its facilities for the production of sustainable platform chemicals in Groningen, the Netherlands.
BioBTX was the first to make 100% bio-based PET, as demonstrated by the cosmetics container lids and winning the Bio-based Innovation award Europe 2016.
The company has been selected by The Sustainable Packaging Coalition and The Center for the Circular Economy at Closed Loop Partners among five entrepreneurs and start-ups that are capable of successfully recovering multi-material flexible packaging waste for new applications.