Want to know more about this article?
Senbis Aims to Stop Microplastic Pollution from Clothing with Biodegradable Polyester, with AI Assistance
Finding a biodegradable replacement for polyester in clothing is considered the holy grail in the fight against plastic pollution. The Dutch R&D company Senbis aims to bring such a product to market by 2030. For the first time, artificial intelligence (AI) will be used to significantly speed up the entire development process.
Source: Change inc.
Every year, the world produces 30 million tons of polyester for clothing. Through washing and wear, a large portion of this ends up as microplastics in the environment, in oceans, and eventually in fish, food, and our bodies. Through the BIOTTEK project, Senbis seeks to develop a biodegradable alternative to polyester in clothing to combat this large-scale pollution. The project involves a consortium that includes the University of Groningen (RUG), NHL Stenden University of Applied Sciences, Wageningen Food & Biobased Research (WUR), and TNO. The consortium is investing 6.6 million euros in developing biodegradable polyester and received a 3.3 million euro grant from the European Just Transition Funds (JTF) last October.
Affordable Alternative
“Polyester is the most widely used material in our clothing, and its use is growing. This poses a huge global problem. Our main goal is to find a solution to all this microplastic pollution,” says Gerard Nijhoving, director of Senbis. “The bioplastics currently on the market aren’t suitable for making good yarn to replace polyester in textiles. Another commonly used material, cotton, is biobased, but when you consider the amount of water and pesticides needed to grow it, it’s not very sustainable. So, a new polymer needs to be developed that is highly scalable, so we can eventually match the price level of polyester. Otherwise, we won’t be able to meet the massive market demand.”
AI Can Help
Inventing and scaling up a new plastic (or polymer) is time-consuming and requires long-term commitment. Nijhoving points to the Dutch company Avantium, which has been working on this for twenty years. Only now is the company building a large factory for its FDCA, a raw material for PEF—a fully plant-based plastic alternative to PET. To accelerate this process, Senbis is using AI for the first time. The company has partnered with TNO, which uses AI and algorithms to identify the most suitable bioplastics. Here’s how it works: currently, knowledge and ideas about new plastics are in the minds of scientists and chemists, who further investigate them through trial and error. “But no one has all the data in their head and can see all the correlations. AI can,” says Nijhoving. “We feed the model with all the relevant polymers we know and their properties. AI can identify all the correlations between them, draw conclusions, and make suggestions for new structures that have exactly the properties we want.”
Completely New
Thanks to AI, Senbis can see much faster whether a material resembles polyester, is biodegradable, and isn’t too expensive to produce. According to Nijhoving, the question to TNO came at the right time, as the institute had just proposed using AI in the development of new materials. “The method of using AI to develop a new type of bioplastic is completely new in the industry and the world. If this works, we will not only have successfully developed a new bioplastic, but we will also have developed a new methodology to accelerate future innovations,” says Nijhoving.
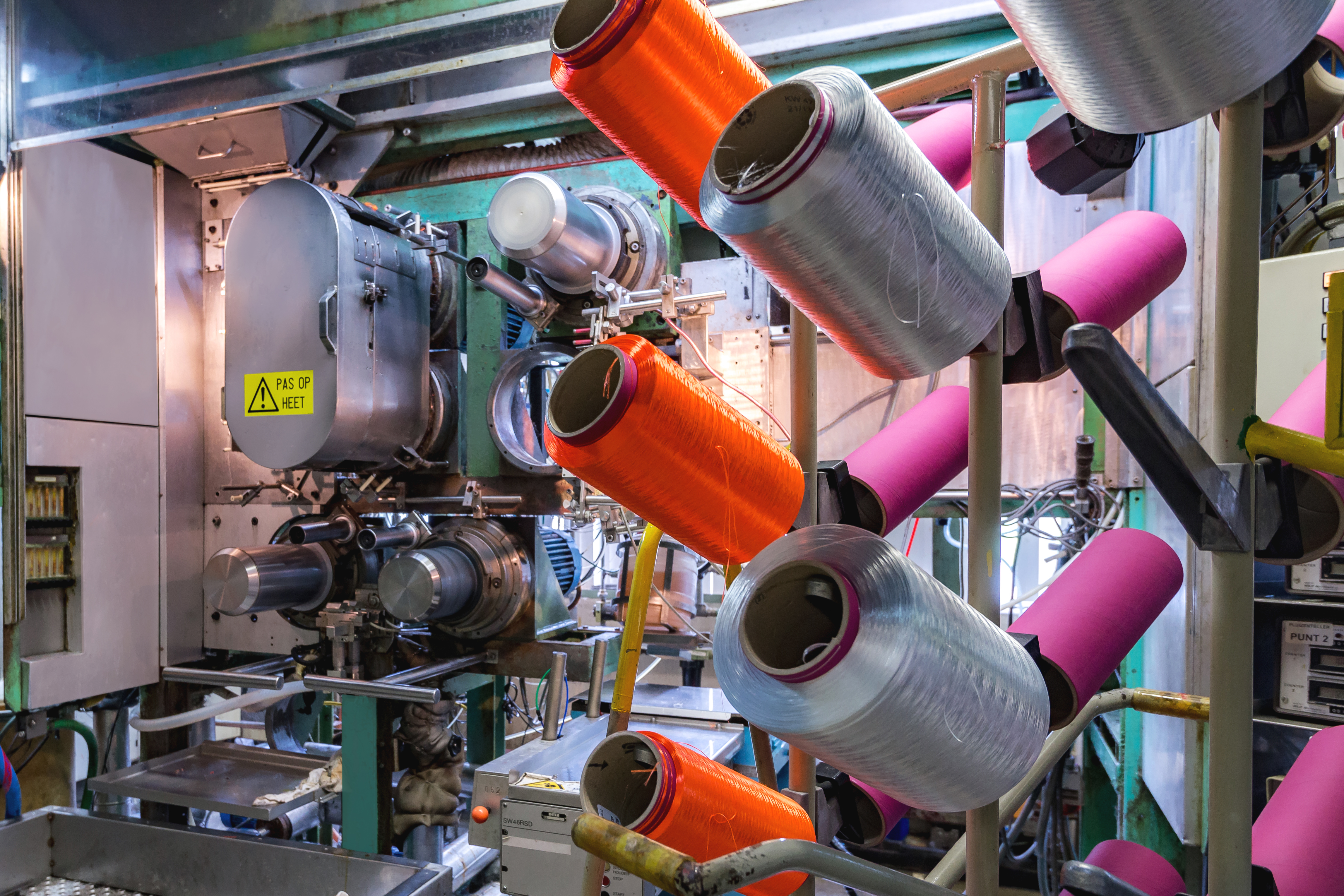
Faster Scaling
Senbis Polymer Innovations—its official name—seeks to solve problems with plastic pollution. The company develops biodegradable plastics for fishing nets and ropes, biodegradable threads and ropes for agriculture, and biodegradable pellets for artificial turf in sports. The company is a continuation of the former R&D department of AkzoNobel in the field of yarn and fibers. R&D activities are carried out by Senbis Polymer Innovations BV, and since 2021, the newly developed products are sold by Senbis Sustainable Products BV. The company doesn’t build its own factories but develops materials in its R&D labs and test facilities, which are then produced and marketed by existing factories under license or contract manufacturing.
“We use existing factories and raw materials that are already available. This limits your search, but you don’t have to build new factories. That takes a long time and costs a lot of money. By working within these constraints, you can scale quickly and make it affordable,” explains Nijhoving.
In-House Expertise
The partners in the BIOTTEK consortium each contribute to the research in their own way. “We brought them together because of their unique expertise,” says Nijhoving. Senbis itself handles most of the research. TNO provides the AI. The RUG was brought in because it has a large chemistry faculty with extensive lab capacity and many researchers who can help in the search for a new polymer. NHL Stenden has a hybrid department where students conduct research at different levels, such as on the recyclability of the new biopolyester. The WUR researches the biodegradability by bacteria and fungi, tests that can take months or years. Since all variants for a biopolyester need to be tested, the research could take a long time. Therefore, WUR has built special reactors where many different samples can be tested simultaneously, which also saves a lot of time,” says Nijhoving.
Market Launch in 2030
The first promising materials for biopolyester have already been identified, although they are still in the minds of the researchers. Nijhoving expects BIOTTEK to select the first good candidates for scaling up and testing yarn quality in spinning by the end of 2025. This is the goal of BIOTTEK, which will conclude with these results. Further research will focus on scaling up and improving the biopolyester to create clothing. Many improvements will be necessary before the material can be marketed. Nijhoving says, “Then you’re ready to take over the world. My ultimate goal is to be able to say in 2030: this is the polymer, it works, it’s scalable. Now we’ll work with large industrial partners to see if they can start mass-producing the new biopolyesters in their factories under license. I think this is a realistic timeline. If it works, it will have been much faster than what typical chemistry startups achieve.”
Microplastic Pollution
Polyester in clothing is one of the biggest sources of microplastic pollution. Research from the University of Plymouth shows that a single 6 kg load of laundry releases more than 700,000 microplastic fibers into the water. This amounts to an estimated 500,000 tons per year. Microplastics are found everywhere: in oceans, fresh snow in Antarctica, and even in the human body. People consume an average of 11,000 pieces of microplastic per year through fish or shellfish, according to researchers in Ghent. Two years ago, they were found in human blood for the first time. Not to mention all the animals that are poisoned or suffocated by plastic.
Green Chemistry Accelerator
This year, Senbis was one of five participants in the Green Chemistry Accelerator program (GCA) of Green Chemistry New Economy (GCNE). This platform aims for circular chemistry with innovative technologies, without fossil fuels and raw materials, and without CO2 emissions by 2050. The GCA program was set up with Invest-NL and the Regional Development Agencies (ROMs) to help startups scale up to fully-fledged companies so they can build pilot plants, enter the market, and ultimately produce thousands of tons of recycled or biobased plastic.
Innovation Funnel
Although Senbis is further along than other startups, it also wants to scale its technology and grow rapidly. This raises questions such as: how do you build a team in chemistry? What does the entire ecosystem around your product look like? Nijhoving has gained a lot of knowledge about this. He also developed an innovation funnel with experts. The R&D company receives more ideas for innovations than it can handle. “So, we have to filter them. Then they go into the funnel. Our R&D people get excited when a cool idea comes in that we can technically work on. But you also have to answer other questions. Is the market big enough? Is there a willingness to pay extra for green alternatives? Are there any patents in the way? With such a funnel, the process becomes much calmer, and we can be more critical. You can’t do everything. This process is now documented, and the GCA helped us build this model.”